Bubble Deck Slab – Types, Material Specification, Installation, and Advantages
Basic Principal of Bubble Deck Slab
The basic principle characteristic is that hollow plastic spheres are incorporated in the floor, clamped in a factory-made reinforcement structure to virtually eliminate all concrete from the middle of a floor slab not performing any structural function, thereby dramatically reducing structural dead weight.
In this article, we study the types, material specifications, installation, advantages, and applicability of bubble deck slabs.
Types of Bubble Deck Slab
1. Type A – Filigree Elements
Bubble deck Type A is a combination of constructed and unconstructed elements. A 60 mm thick concrete layer and part of the finished depth are precast and brought on-site with the bubbles and steel reinforcement unattached.
The bubbles are then supported by temporary stands on top of the precast layer and held in place by interconnected steel mesh. This type of bubble deck is optimal for new construction projects where the designer can determine the bubble positions and steel mesh layout.
2. Type B – Reinforcement Modules
The bubble deck Type B is a reinforcement module that consists of a pre-assembled steel mesh and plastic bubbles. These components are brought to the site, laid on traditional formwork, connected with any additional reinforcement, and then concreted in place by traditional methods.
This category of Bubble Deck is optimal for construction areas with tight spaces since these modules can be stacked on top of one another for storage until needed.
3. Type C – Finished Planks
The bubble deck Type C is a shop-fabricated module that includes the plastic spheres, reinforcement mesh, and concrete in its finished form. The module is manufactured to the final depth in the form of a plank and is delivered on-site.
Unlike Type A and B, it is a one-way spanning design that requires the use of support beams or load-bearing walls. This class of Bubble Deck is best for shorter spans and a limited construction schedule.
Material and its Specifications used in Bubble Deck Slab
1. Concrete
The concrete used for joint filling in the Bubble Deck floor system must be above M20-25 grade. The nominal maximum size of the aggregate is the function of the thickness of the slab.
Usually, self-compacting concrete is used, either for the casting of prefabricated filigree slab or for the joint filling on the site. Self-compacting concrete can be poured into forms, flow around congested areas of reinforcement and into tight sections, allowing air to escape and resist segregation.
2. Reinforcement Bars
The reinforcement of the plates is made of two meshes, one at the bottom part and one at the upper part that can be tied or welded. The steel is fabricated in two forms, the meshed layers for lateral support and diagonal girders for vertical support of the bubbles.
The distance between the bars is corresponding to the dimensions of the bubbles that are to be used and the quantity of reinforcement from the transverse ribs of the slab. Grade Fe-500 strength or higher is used.
3. Hollow Bubbles
The bubbles are made using high-density polypropylene materials. These are usually made with a non-porous material that does not react chemically with the concrete or reinforcement bars.
The bubbles have enough strength and stiffness to support between 180mm to 450mm. Depending on this, the slab depth is 230mm to 600mm. The distance between bubbles must be greater than 1/9th of the bubble diameter.
The nominal diameter of the gaps may be 180, 225, 270, 315, or 360 mm. The bubbles may be spherical or ellipsoidal.
Installation of Bubble Deck Slab
The overall floor area is divided down into a series of planned individual elements, up to 3 m wide dependent upon site access.
These elements comprise the top and bottom reinforcement mesh, sized to suit the specific project, joined together with vertical lattice girders with the void formers trapped between the top and bottom mesh reinforcement to fix their optimum position which is termed as a bubble-reinforcement sandwich.
The bottom layer of 60 mm pre-cast concrete is cast, encasing the bottom mesh reinforcement, to provide permanent formwork within part of the overall finished slab depth.
On-site the individual elements are then ‘stitched’ together with loose reinforcement simply laid centrally across the joints between elements.
After the site finishes, concrete is poured and cured.
This technique provides structural continuity across the entire floor slab – the joints between elements are then redundant without any structural effect, to create a seamless biaxial floor slab.
Advantages of Bubble Deck Slab
1. Superior Statics
Bubble deck slab has superiority over the conventional slab as it has reduced weight, increased strength, fewer columns, and no beams or ribs under the ceiling.
2. Production and Carrying Out
The production is of higher quality through the automated production of prefabricated units. Minimum work at the site removes the possibility of errors and the lightweight of the slab helps in easier erection with light and cheap lifting equipment.
3. Transportation
The transportation of materials is reduced considerably. Thus, lower costs, and environmental improvement.
4. Economic Savings
The major savings are found in materials (slabs, pillars, fundaments) up to 50 %. Due to its lightweight, transportation costs are heavily reduced.
5. Safety
The bubble deck slab is fireproof and the safety against earthquake is significantly benefited Fire – Fireproof construction alone from the weight reduction.
6. Environmental Improvement
With the use of the bubble, 1 kg of plastic replaces more than 100 kg of concrete. Energy consumption for production, transport, and carrying out is very less. Thus, less emission of CO2.
7. Explosions Safe
Bubble Deck’s biaxial flat slab system and columns are ideal for structures with high resistance against explosions. To get rid of heavy facades and rigid walls, suppressing air pressure which in the worst case leads to the collapse of the structure.
Residential living, offices, utility, and industrial buildings. Used in offices, apartments, villas, hotels, schools, parking, hospitals, laboratories, and factories.
About Author:
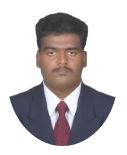
I am Thomas Britto here to share my experiences in the civil engineering field to all my readers.Today many students are struggling to buy books at high prices. So I decided to start a blog and share my experience and knowledge with all my readers.
Let's Get Connected: Twitter | Facebook | Google Plus
No comments
Post a Comment